»MultiSkive«: design principles for multi-cutting strategies.
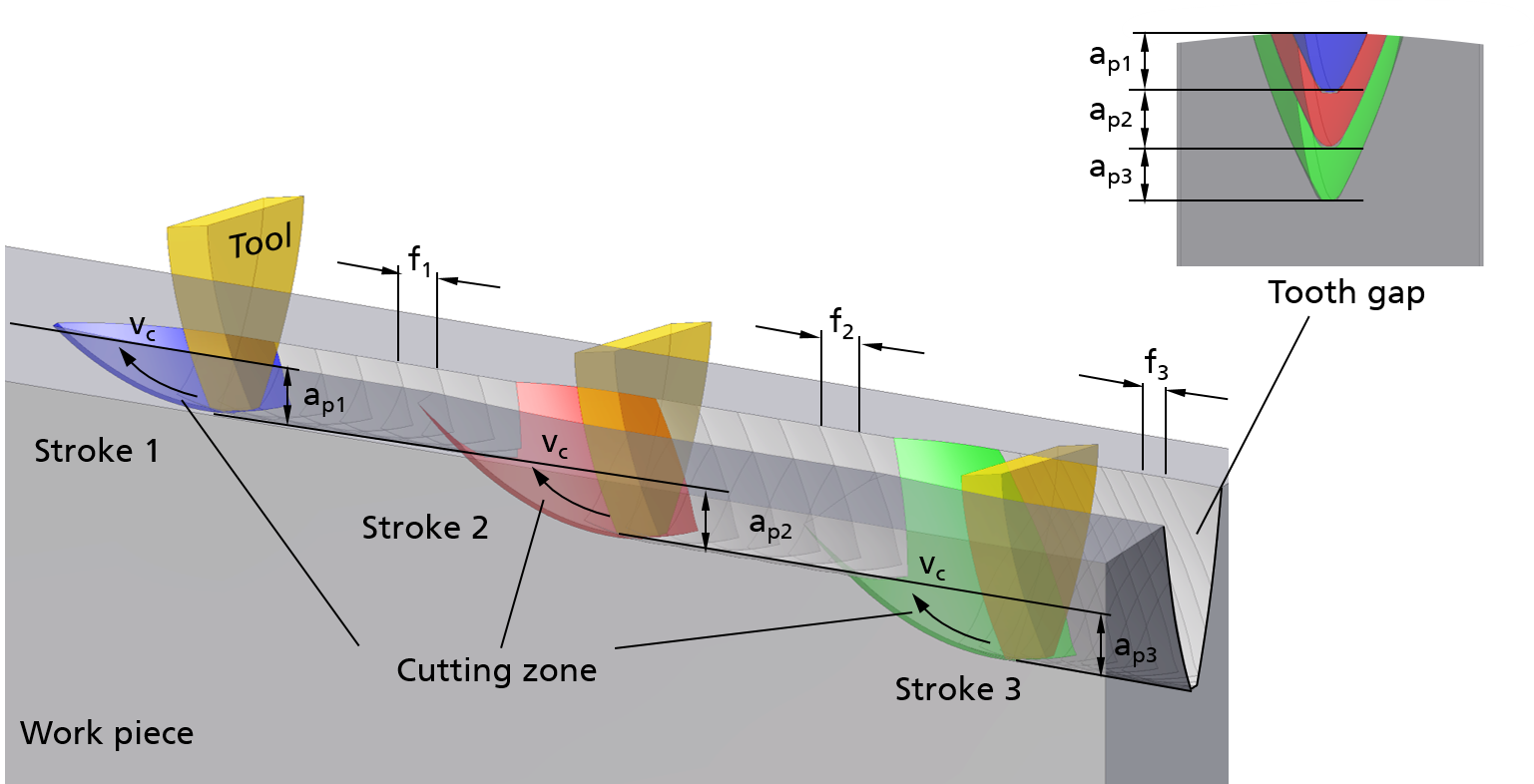
According to the current state of research, the use of multi-cutting strategies is unavoidable in Power Skiving. The reason for this is the tendency towards strongly negative rake angles with increasing depth of cut.
Due to the considerable number of cuts, the number of degrees of freedom in the process design also increases - however, a uniform calculation model is lacking. In a current research project, this gap is to be closed.
To this end, basic tests are being carried out on the influences of the most important productivity-determining design parameters of cutting depth / number of cuts and feed rate.
Based on the results, a model for tool load and chip formation is to be developed, which should make a more precise design of multi-cutting strategies possible in the future.